I recently ordered some
wired Red and Warm White 0605 Bi-colour SMD LEDs on ebay for marker lights as I really don't like the red/cool white versions we seem to get on our locomotives.
When they arrived, I sat down to use them as marker lights on a Trainorama 44 Class and realised that I had a problem.
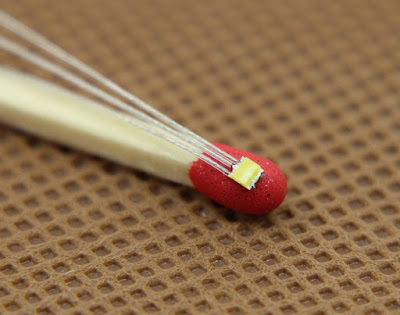 |
Size of a 0605 Bi-colour SMD LED |
Just before I ordered them I was looking at
wired RED and White 0605 SMD Bi-colour LEDs from the same supplier and had noted that they were wired with a Common Anode.
Well, you can probably guess by now what my issue was, yes, the Red/Warm White ones were Common Cathode!
Why is this a problem?
DCC decoders are designed for Common Anode, so if I had used the LEDs as they came I would have ended up with both Red and Warm White turned on at the same time.
So, I was left with little option but to rewire them. I had bought the wired ones to avoid just this scenario!
I bought a
magnifying glass on a gooseneck from JayCar Electronics that has a small 5 X lens in the larger 2X lens, more expense but it will be useful I guess.
I took a piece of Bostik Blue Tak, made a small 1 cm ball of it and pushed it onto my workbench. Into this I pressed the 'lens' side of the 0605 LED exposing the wire connections on the rear.
I placed the magnifying glass so that I could see the LED through the 5 X lens.
I have a temperature controlled soldering iron with a very fine point which I used to unsolder the three wires.
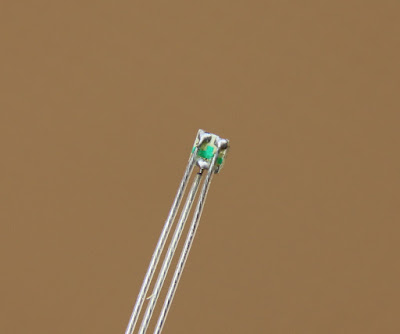 |
Rear of a 0605 SMD Bi-colour LED - Correct Anode Common wiring |
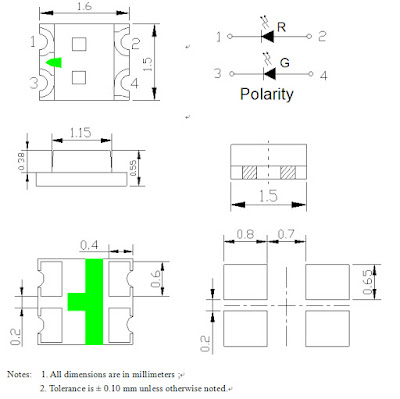 |
0605 SMD Bi-colour LED Circuit |
As can be seen from the circuit above there are simply four contacts, one in each corner to solder to which made the rewire easier.
I took one of the two long wires and soldered it across the opposite two contacts than the ones that had previously been bridged. This now formed the Common Anode connection.
I shortened the long wire to the same length as the remaining wire to form the two Cathode wires and soldered them in place.
The first one took about 30 minutes of stuffing about but I can now do them inside of 5 minutes. So far I have done five.
I did try double sided tape first but I found that the LED moved around too much, the Blue Tak holds better as the 'lens' can be pushed into the Blue Tak for a better bond.
I don't know if all RED/Warm White 0605 Bi-colour SMD LEDs are Common Cathode, probably not, but I made this post to make the modeller aware of a potential issue.
Oh, yes, how many did I buy?
40!
And no, I haven't installed them as yet, took the wind out of my sails a bit, not an uncommon thing of late.